FNT Technologies
At FNT we exploit and combine the following Predictive Maintenance technology:
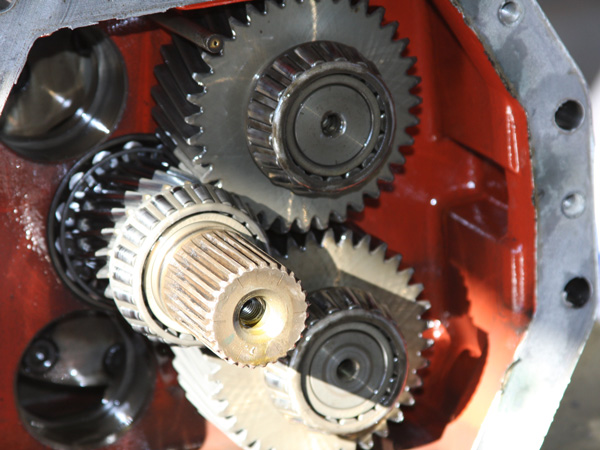
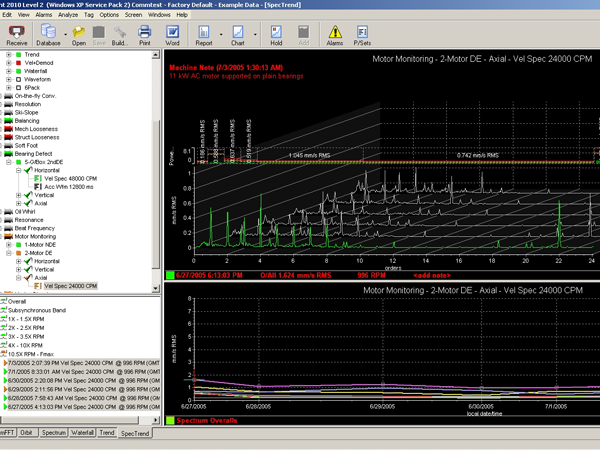
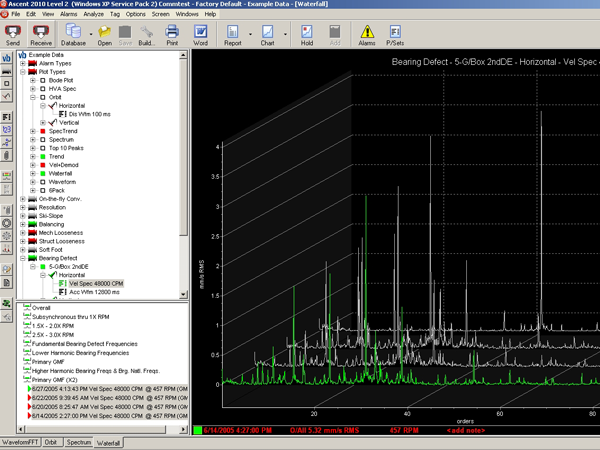
Vibration Measurement and Analysis
One of the most widely used techniques in condition based maintenance. It is mainly used to evaluate the condition of rotating machinery. Machine vibrations stack a lot of information about the condition of a machine. Each individual element in a rotating machine vibrates at characteristic frequencies. The detection of each element frequency and the qualitative and quantitative analysis provides machinery condition evaluation, i.e. a bent shaft will always peak at twice the rotation speed frequency, while a ball bearing might vibrate at 20 times the rotation speed frequency.
The prime notion behind the use of vibration analysis is to monitor rotating machinery to detect growing problems and to eradicate the possibility of a catastrophic failure. This is the most widely used maintenance practice applied in strategic maintenance systems.
Oil Particle Counting and Cleanness Monitoring
The concentration of wear particles in oil is a key indicator of potential component problems. Therefore, oil analysis must be capable of measuring a wide range of wear particles and contaminant particles. Oil Particle Counting is considered by many to be the single most important test for used oil analysis. Particle count data is an invaluable part of any proactive condition-monitoring program, from ensuring that abrasive bearing wear is minimized, to determining if a hydraulic fluid is clean enough for reliable operation.
The most common unit of reporting fluid cleanness is the ISO Code System. This convention is covered under the ISO 4406:99 standard. Oil cleanness index is monitored based on scheduled oil sample analysis. The resulting index trend is interweaved and correlated with findings from other condition monitoring technologies, such as vibration analysis, in order to accurately evaluate machinery condition.
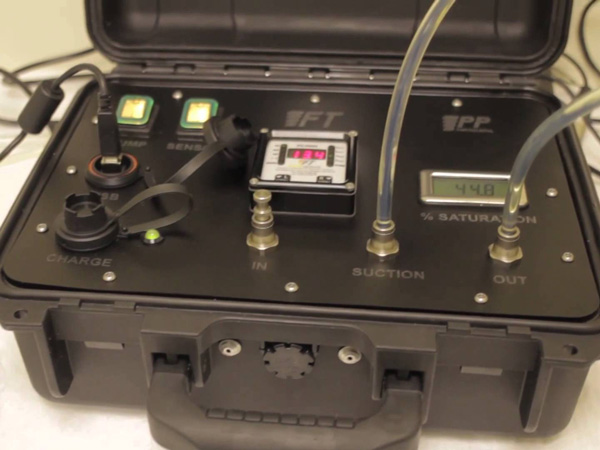
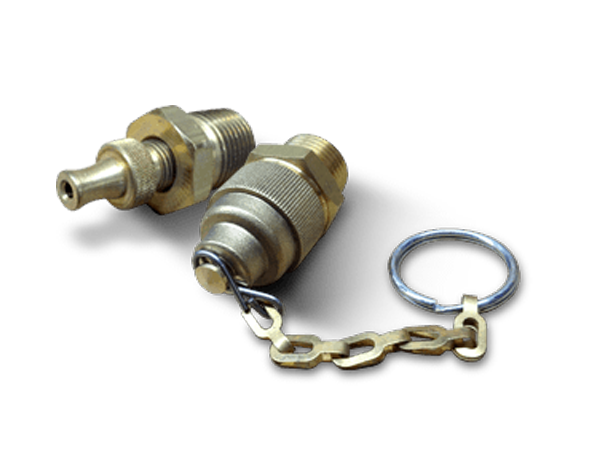
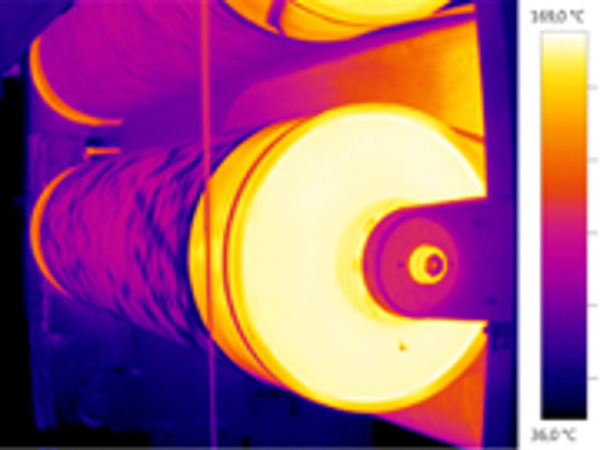
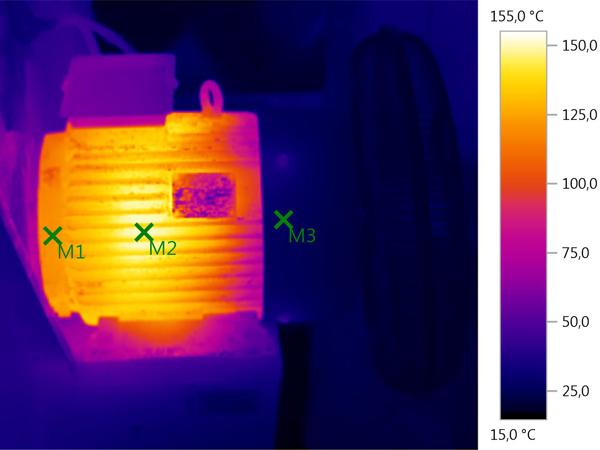
Thermal Imaging
Thermal imaging or infrared thermography is a nondestructive maintenance method that uses infrared cameras to measure the amount of thermal radiation emitted by objects, which is converted to temperature. Changes in heat will graphically display problem areas where wear is taking place or where there is an excessive resistance in an electrical circuit.
Thermal imaging is applied for fault detection in the following areas:
- Electrical equipment (earth faults, circulating currents, laminations cracking insulation, phase imbalance, electrical connections overheating, motor winding overheating, etc).
- Mechanical equipment (misalignment or bent shafts and damaged bearings detection, frictional heat due to insufficient lubrication, tank level measurement, etc).
In general the main advantage of thermal imaging is that we can inspect electrical equipment live quickly and easily without changing the operating condition of the plant thus eliminating the danger of an accident.
Motor Current Signature Analysis (MCSA)
MCSA uses the electric motor as a transducer, in order to evaluate the electrical and mechanical condition. The current signal is acquired from one phase of the motor supply (at motor terminal box, or at local electric panel) without interruption of the machine operation. In MCSA the current signal is processed to obtain the frequency spectrum usually referred to as current signature. By means of the motor signature, one can identify the magnitude and frequency of each individual component that constitutes the signal of the motor.
The analysis of the results helps in identifying problems at motor rotor bars, rotor eccentricity, stator windings, motor bearings and coupling defects. IMCSA is an extremely useful technology for CM of motors and their loads enclosed in casing (such as E/R fans and Cargo Hold Fans) as well as in cases where there is restricted access to the motor.
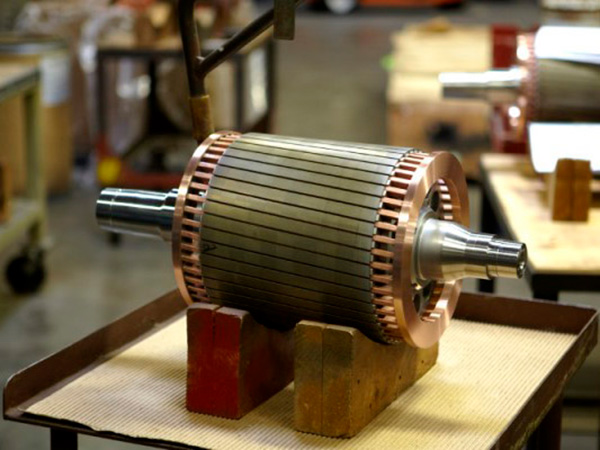
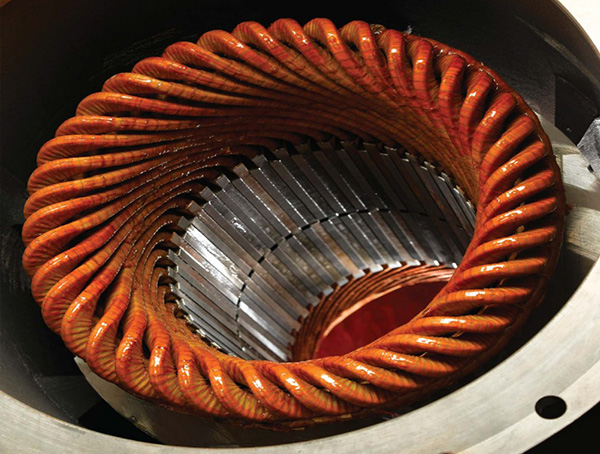
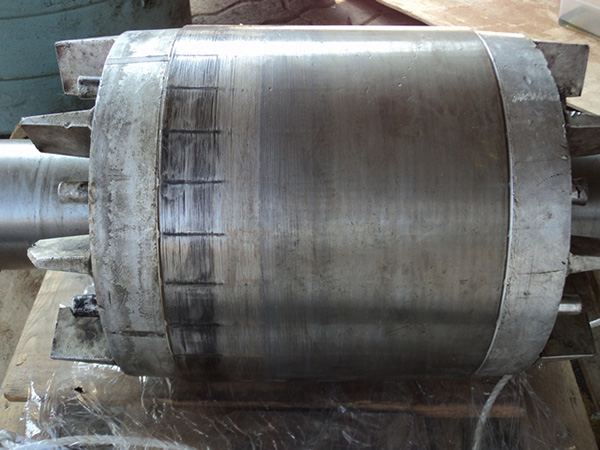
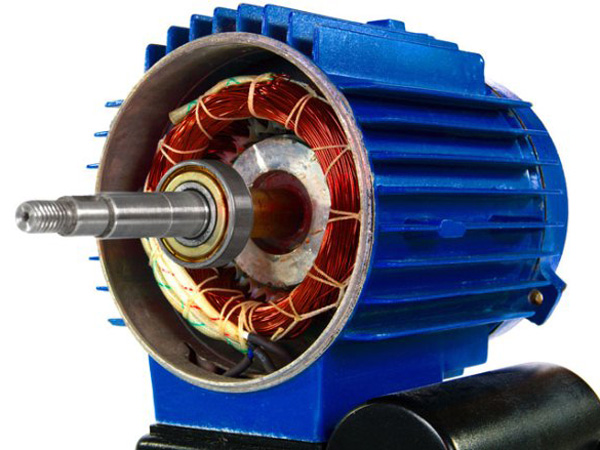
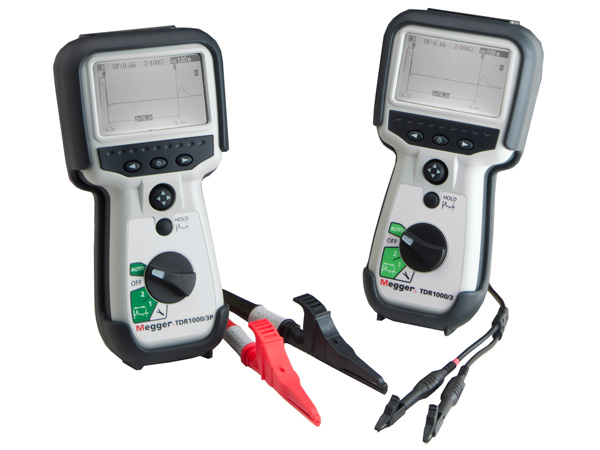
Motor Current Evaluation
Motor testing is conducted in order to improve motor reliability, thereby decreasing the risk of failure. The Insulation Resistance (IR) of an electrical system degrades with time, or due to environmental conditions i.e. temperature, humidity & dust particles. It also get impacted negatively due to the presence of electrical & mechanical stress, so it’s become very necessary to check the IR of equipment at a constant regular interval to avoid any measure fatal or electrical shock. Megger is the device that enables us to measure reliably electrical leakage in wires.
Additionally, Insulation Resistance Test (IR Value Test) and Polarization Index Test (PI Value Test) are conducted in order to determine the condition of the insulation (dryness and cleanliness) at high voltage machines where the windings are also likely to be affected by moisture and contamination.
Acoustic Emissions & Ultrasonic
Most machines emit consistent sound patterns under normal operating conditions. These sound patterns (sonic signatures) can be defined and recognized, and therefore changes in these signatures can be seen as signs of wear or deterioration. In a certain sense, it is a different form of mechanical vibrations. Acoustic Emission analysis is a useful technique in providing early warning in cases of:
- Leak detection in pressure and vacuum systems
- Bearing inspection
- Bearing lubrication
- Steam trap inspection
- Pump cavitations
Acoustic Emission is a quick technique for bearing condition survey especially for factory plants with many rollers and gives excellent results if it is coupled with vibration analysis.
Additionally, it is an excellent tool to be used in bearing lubrication programs.
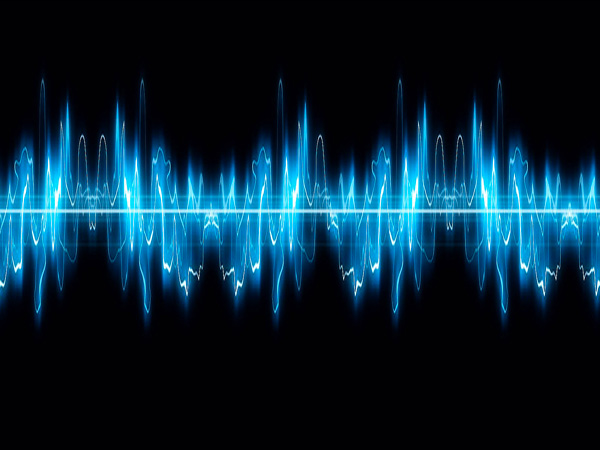